Green hydrogen removes 98% of the carbon dioxide produced in conventional steel manufacturing.
Luleå in the far north of Sweden is an unlikely place for a revolution. The town has a strong heavy-industry heritage, and is also a garrison for the Swedish air force. It is otherwise a peaceful place. But Luleå also has access to plentiful hydropower energy. It is this particular asset that has made it so attractive to SSAB, a steelmaker that has developed a truly transformative production process.
“What the Hybrit project shows is that, sometimes, you have to change quite fundamentally the whole mode of production to decarbonise heavy industries.”
– Jon André Løkke
Green hydrogen is key
SSAB’s Hybrit project uses Nel’s water electrolyser technology to produce green hydrogen. This gas replaces the methane that is used in conventional steelmaking to reduce, or break down, iron-oxide ore to iron. The new hydrogen-based method removes almost all greenhouse-gas emissions from a metal-making industry that is crucial to the world economy, but has long been seen as one of the most difficult to decarbonise.
For many years, there was discussion about capturing carbon dioxide from steel-factory flues, and storing this planet-heating gas underground. Besides being a costly approach, it is also one fraught with difficulties and dangers—chiefly the problem of ensuring that, once sequestered, the gas does not then leak out again to contribute to further global warming.
“What the Hybrit project shows is that, sometimes, you have to change quite fundamentally the whole mode of production to decarbonise heavy industries. Alongside steel, we see similarly big gains to be made in sectors like cement and fertiliser production, all by virtue of using green hydrogen,” says Jon André Løkke, CEO of Nel.
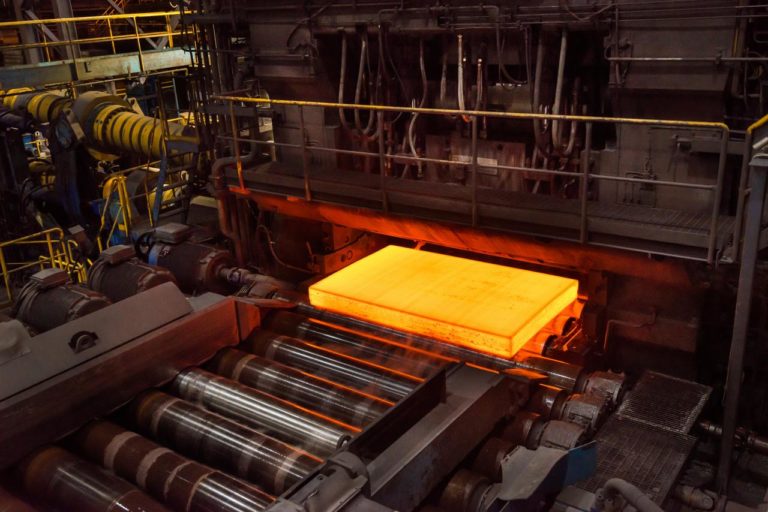
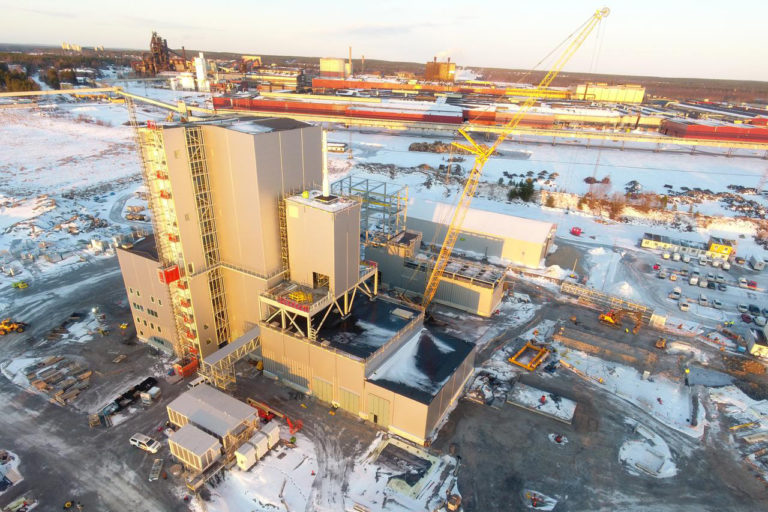
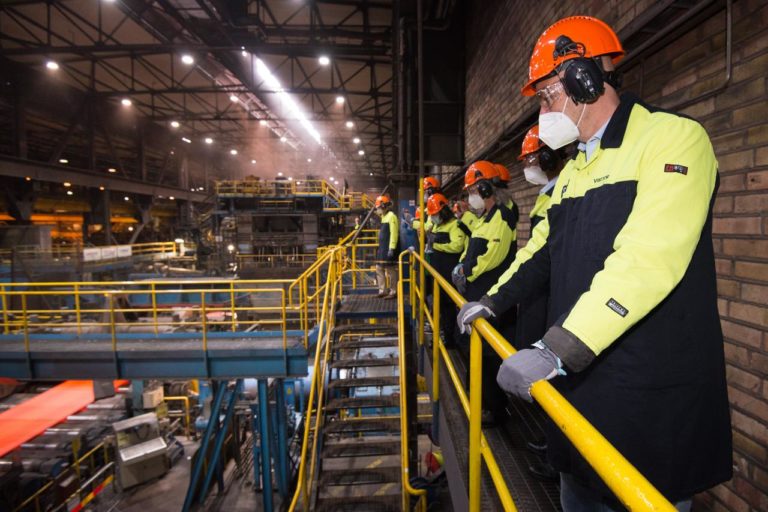
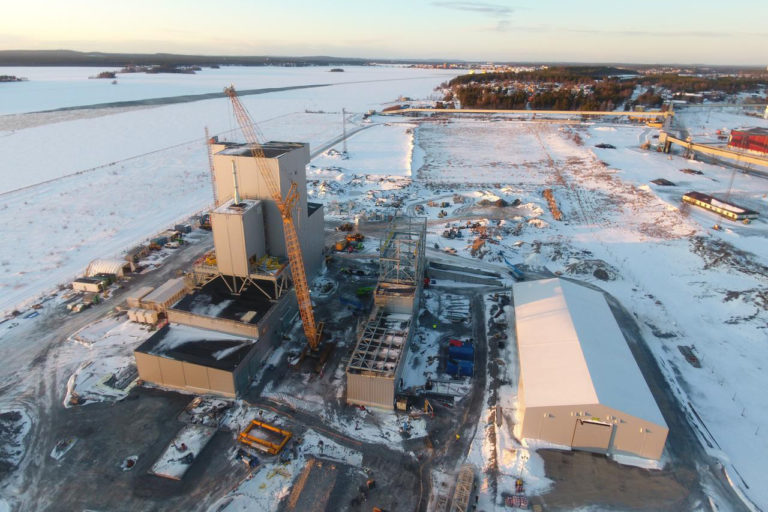
Decarbonising the automotive supply chain
The implications of the Hybrit project’s innovations are huge. Europe alone produces 16% of the world’s steel, and much of it comes from Germany and Poland where the energy mix is already highly polluting. Given Europe’s dominance in vehicle manufacturing, the opportunities for reducing carbon-dioxide emissions across the supply chain are clearly significant. Around 70% of a commercial vehicle’s weight comes from steel.
Already in Sweden, Volvo has made the world’s first fossil-free-steel vehicle, an achievement that the company describes as “setting the benchmark” for a future of safe and efficient vehicles for more sustainable transport and infrastructure. Volvo’s load carrier for use in the mining industry was unveiled in October last year.
In June this year, the company will hand over its first green-steel vehicle to a paying customer. Scania, another Swedish vehicle manufacturer, has similarly ambitious plans, and can also look forward to producing its vehicles using SSAB’s green steel. Scania has also invested in H2 Green Steel. This second hydrogen-based steel plant is planned to be constructed in Boden, a town around 30km to the north-west of Luleå.